
Sony uses Triniti Product Modeler (TPM) to Manage New Product Introduction and to Efficiently Maintain Supply Chain Data
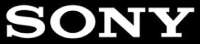
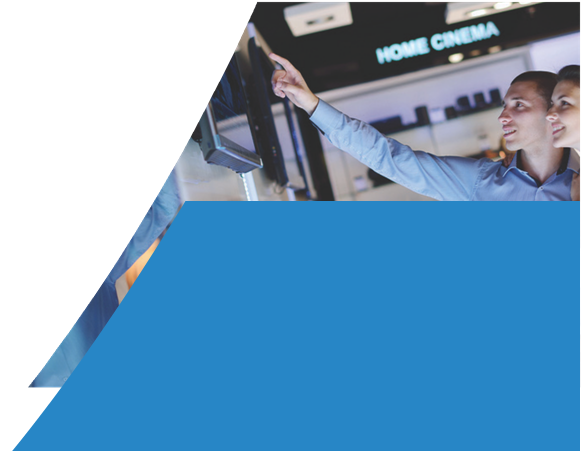
Client Background
Sony Corporation is a Japanese multinational conglomerate, headquartered at Konan Minato, Tokyo, Japan. It is one of the leading manufacturers of electronic products for consumer and professional markets
"In our i-Semicon (Oracle Application Implementation) project, we have implemented a Triniti productivity tool named ‘Triniti Product Modeler’ aimed at substantial improvements in the speed and accuracy of creating and maintaining the complete Supply Chain (Item, Bill of Materials, and Sourcing Rule). Today, our users can create, edit, and revise complex bills of materials in a fraction of the time it would take otherwise"
- Shuji Kuroki, Global Master Center Lead, Sony Semiconductor, Kyushu Corporation
Outcomes
TPM’s functionalities as an application management tool positively impacted Sony’s efficiency and performance by helping users create and maintain Timely, Reliable, Accurate, and Complete (TRAC) master data. As a result, Sony was able to:
- Accelerate setup times and increase productivity with TPM’s single window setup design and Mass Update feature
- Facilitate collaboration among its supply chain teams for faster and more accurate New Product Introduction with TPM’s workflow
- Increase ability to adapt to changing business requirements with TPM’s quick configuration ability
- Enhance re-usability using TPM’s Supply Chain Models
- Visual confirmation of a fully built supply chain bill
- More than 100 end users collaborate to create product master data
Business Challenges
While implementing Oracle eBusiness Suite, it became evident that maintaining the complex supply chains would be an arduous task. Sony was experiencing the following problems in its Supply Chain setup and business processes:
- Manual maintenance would have needed an army of users to keep up with the high volume and complex supply chain
- Navigating through multiple Oracle screens (up to 30 screens) is cumbersome, time-consuming, and prone to errors
- Long turn-around times for Supply Chain BOM setups and maintenance
- Lack of a system to track and audit collaboration between different teams would have resulted in longer turnarounds, low visibility, and poor data quality
Solution Highlights
Triniti conceptualized and developed TPM at Sony as a tool to provide a single screen for creating, modifying, and viewing the complete supply chain. Triniti performed the following using TPM:
- Drag and drop Nodes and Relations to represent the different BOM levels and linkages in the supply chain
- Created TPM Models to store Supply Chain structure templates along with node-specific attributes which can be reused to set up new supply chain bills
- Mapped the elaborate and complex New Product Introduction (NPI) process in TPM using in-built workflows
- Controlled data access using role-specific security
- Significantly decreased the setup time for supply chains
- Significantly reduced errors in data entry
Complex Supply Chain Created in TPM